在制造業(yè)現(xiàn)場(chǎng)管理中,我們經(jīng)常遇到一個(gè)令人頭疼的現(xiàn)象:車間員工看起來很忙碌,但整體生產(chǎn)效率卻始終提不上去。這種"假忙"現(xiàn)象不僅影響企業(yè)效益,還會(huì)打擊員工士氣。今天我們就來深入分析造成這種現(xiàn)象的8個(gè)關(guān)鍵原因,幫助管理者找到問題根源,實(shí)現(xiàn)真正的效率提升!原因一:生產(chǎn)流程設(shè)計(jì)不合理
很多工廠的生產(chǎn)流程還停留在"經(jīng)驗(yàn)主義"階段,缺乏科學(xué)規(guī)劃。常見問題包括:解決方案:運(yùn)用價(jià)值流圖(VSM)分析整個(gè)生產(chǎn)流程,識(shí)別并消除非增值環(huán)節(jié),重新優(yōu)化車間布局。解決方案:實(shí)施5S管理,建立可視化物料標(biāo)識(shí)系統(tǒng),推行準(zhǔn)時(shí)化(JIT)物料配送。老舊設(shè)備或缺乏保養(yǎng)的設(shè)備是效率殺手:設(shè)備突發(fā)故障造成產(chǎn)線停滯解決方案:推行TPM全員生產(chǎn)維護(hù),建立預(yù)防性保養(yǎng)計(jì)劃,逐步淘汰高故障率設(shè)備。新員工占比高或培訓(xùn)不到位會(huì)導(dǎo)致:操作不熟練,節(jié)拍時(shí)間延長(zhǎng)解決方案:建立標(biāo)準(zhǔn)化作業(yè)指導(dǎo)書(SOP),實(shí)施師徒制培訓(xùn),定期開展技能比武。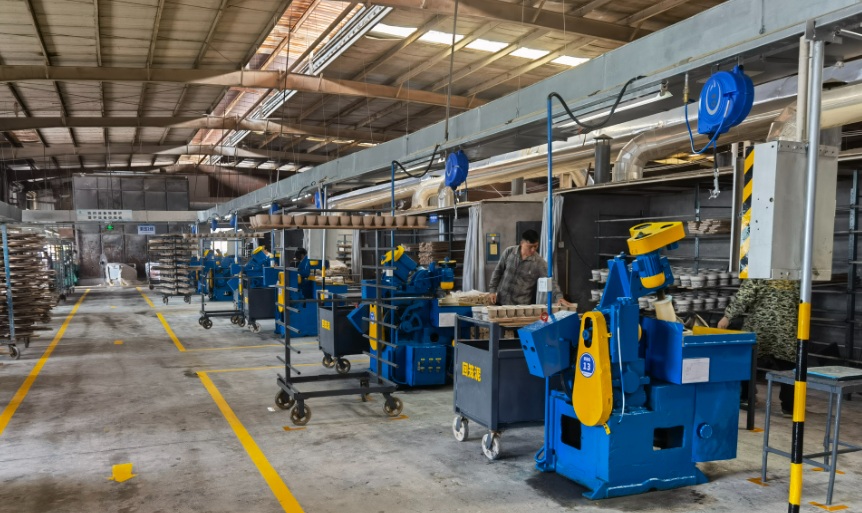
拍腦袋式的生產(chǎn)計(jì)劃會(huì)造成:頻繁換產(chǎn),設(shè)備調(diào)試時(shí)間長(zhǎng)解決方案:導(dǎo)入高級(jí)計(jì)劃排程系統(tǒng)(APS),建立最小生產(chǎn)批量標(biāo)準(zhǔn),優(yōu)化換模流程。原因六:績(jī)效考核導(dǎo)向錯(cuò)
考核方式會(huì)引導(dǎo)錯(cuò)誤的行為:單純考核工時(shí),忽視產(chǎn)出質(zhì)量團(tuán)隊(duì)績(jī)效與個(gè)人貢獻(xiàn)脫節(jié)解決方案:建立以O(shè)EE(設(shè)備綜合效率)為核心的考核體系,平衡數(shù)量、質(zhì)量、成本指標(biāo)。松散的管理會(huì)導(dǎo)致各種浪費(fèi):等待、搬運(yùn)、動(dòng)作等隱性浪費(fèi)質(zhì)量問題不能及時(shí)發(fā)現(xiàn)解決方案:推行精益生產(chǎn),實(shí)施走動(dòng)式管理,建立快速響應(yīng)機(jī)制。長(zhǎng)期低效工作會(huì)形成惡性循環(huán):解決方案:建立透明化的績(jī)效溝通機(jī)制,設(shè)計(jì)合理的激勵(lì)方案,營(yíng)造持續(xù)改善文化。結(jié)語(yǔ):從"假忙"到"真效"的轉(zhuǎn)變
車間效率提升是一個(gè)系統(tǒng)工程,需要管理者深入現(xiàn)場(chǎng),用專業(yè)的眼光發(fā)現(xiàn)問題,用科學(xué)的方法解決問題。建議每周選擇一個(gè)重點(diǎn)問題進(jìn)行專項(xiàng)改善,循序漸進(jìn)地提升整體效率。記住:真正的效率不是讓員工更忙,而是讓工作更順暢!
該文章在 2025/4/11 14:32:47 編輯過